The Important Points
- If your iPhone or iPad has a dull screen that doesn’t “light up”, it’s probably a backlight issue. We can fix this! Contact us online for more details or visit our store.
- The backlight is the rearmost layer in the LCD and makes it light up. If the backlight or related circuit fails, the screen will no longer glow.
- Poor-quality copy screens can overload the backlight circuit and cause it to fail after a while. This turns a cheap screen replacement into an expensive repair. We always recommend good-quality refurbished screens where possible.
- Backlights can also fail under “regular” use due to water/liquid damage.
- Backlight circuit repair can be risky in less experienced hands. In addition, if a business cuts its prices too low, it often can’t afford the time- and risk- to do the job properly.
- Many businesses focus on simpler repairs that can be done using by-numbers “parts swapping”. This is fine as far as it goes, but doesn’t work for more complicated repairs.
- Board-level repairs are far more complex and risky, and require far more experience and training. That’s why they cost more and can’t be compared to “parts swaps”.
- We’re not always the very cheapest, but we have years more experience than most of the competition and won’t cut corners with your valuable iPhone or iPad.
Introduction
If your Apple iPhone or Apple iPad is having problems with a dim screen, it’s almost certain that the fault is related to the backlight.
Modern LCD screens have three layers. The LCD panel itself sits in the middle, but on its own this is just an unlit black-and-white display (think of a higher resolution version of the old-style LCDs used in digital watches or early Nintendo GameBoys). At the front, a filter layer adds colour, but it’s the backlight shining from behind that makes your phone’s screen light up. If this backlight fails, your screen will be very dark and only be visible under strong light. However, very often this problem is caused not by the failure of the backlight itself, but by the related “backlight circuit” that powers and controls it. It’s damage to the backlight circuit- rather than the backlight itself- we’ll be concentrating on here.
Fortunately, it’s possible to have these “dim screen” backlight problems repaired. If you don’t want to read this entire article, the short version is- bring it to us. We can often fix the problems that others can’t… and we know how to avoid the mistakes that can lead to them happening in the first place.
Where The Damage Happens- The Backlight Circuit
The backlight itself is powered by the “backlight circuit”. To simplify things somewhat, the main components of this circuit are a coil, backlight IC, diode, filter and some capacitors.
Some newer Apple devices- from the 6S upwards- have the circuit in two parts, one for each side of the screen. If the part associated with one half gets damaged, half the screen will go dull.
(Very occasionally, a dull display can be caused by the FPC connector to the LCD getting squashed, rather than damage to the backlight circuit. However, this is very rare.)
How Copy LCDs Can Damage the Backlight Circuit
Surprisingly, damage to backlight circuitry is often caused by the use of so-called “copy” displays. As we explain in our article on copy screens, these are compatible- but independently designed- replacement displays from third-party companies, and typically fitted as a replacement for a broken iPhone screen.
We’ve heard about people going to a repair shop, getting their screen replaced, then returning a week later after the backlight stops working… only to be told that the two problems weren’t connected. Unfortunately, in cases like these, there’s a high probability they were connected.
Unlike genuine original screens (“OEM”) or refurbished original screens (“Non-OEM”), copy displays are designed and manufactured entirely separately from Apple, and often don’t match the electrical characteristics of the original display. In particular, many copy screens draw much more power than the original displays. This can result in the backlight circuitry being overloaded with far more power than it was designed for- and damaged as a result. If the backlight circuit doesn’t work, the backlight itself won’t light up!
There are many different types of copy screen- some better than others, but typically with lower quality control, especially on the display itself. Other issues include solder points on the screen not having been covered correctly, resulting in them shorting out on the backplate when fitted. Some inexperienced technicians will fail to notice this- again, it can result in damage to the phone.
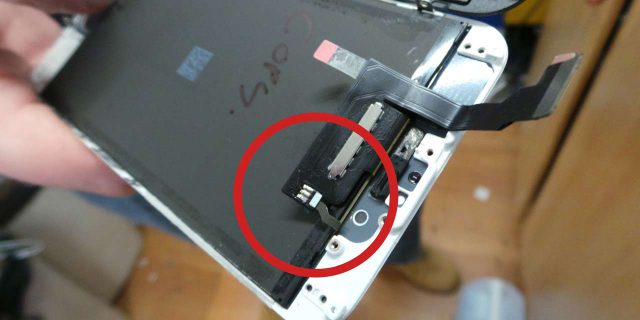
Fixing the Backlight Circuit- Not Always Simple, Often Risky
There’s more than one potential cause of backlight circuit failure, and they’re not all equally simple to fix- some repairs can consist of a simple filter replacement, and others can require replacing the whole circuit or adding jumper wires to bypass damaged tracks. This is easier on some devices than others.
Sometimes extreme current or overvoltage can cause filters to have literally exploded and damaged the solder pad. In addition to the filter replacement, our technician must solder jumper wires to other points in such cases. Damage can also be caused by heat during repair. In order to reduce this risk, some stores and technicians used a CNC to cut the IC away from the board. While this was never particularly common, it’s still done. Problems (and hence damage) can be caused if the CNC programs- designed around a specific circuit layout- contain bugs or errors. However, in principle, there shouldn’t be a risk with this method.
Was the Battery Disconnected Before the Repair?
It’s important to disconnect the battery before connecting or disconnecting the LCD, but on some devices this isn’t possible. With some iPads, you need to remove the display to get to the battery connector in the first place. On some early iPads, the backlight didn’t go as it had some protection built-in where the screen went dull, but could be restored via a hard reset.
Board-Level Backlight Circuit Repair- Harder Than It Looks
As mentioned above, the backlight circuit can be damaged by overload from a badly-designed “copy” screen or if the battery wasn’t properly disconnected before working on the device.
These generally happen during or shortly after a poor-quality repair. However, under regular circumstances, backlight failure generally only happens due to some external factor. This can include water/liquid damage, which can short-circuit the backlight or cause corrosion on the board. Both of these can cause the backlight to fail.
When it comes to phone repair, there are countless such traps for the unwary- and inexperienced- technician. (Even just taking some phones apart can result in damaged ribbons or connectors if you aren’t careful.) The problem is exacerbated when they don’t have the backup of more experienced colleagues to guide them and fix any problems.
Unfortunately, many businesses most likely to be in this position are also those competing on price with narrow margins. Often there simply isn’t the time to investigate and fix board-level damage properly (nor the money to hire another company to fix the issue). The only option is to fix it themselves, but as a result they’ll often have cut corners such as bypassing- rather than replacing- a damaged filter. This appears to work, and the customer takes the (apparently) repaired phone away.
However, filters are generally there for a very good reason! They exist to smooth out signals and currents and- to some extent- may have the side effect of protecting the circuit. Bypassing it may cause problems or even damage to the circuit due to current spikes and so on. Unfortunately, these may happen some time after the repair, so it can be hard knowing- let alone proving- that this was the cause of the problem.
Many times such shortcuts are taken in order to rush the phone out the door before the customer realises there’s a problem. Filters and other components can take time to come in, and when you’re relying on high turnover to keep your head above water you can’t afford more wasted time and customer hassle.
Bypassing the filter is somewhat like replacing a blown fuse in a mains plug with foil… you just don’t do it, no matter how desperate or urgent it is!
Finally, it’s also the case that some technicians are more professional than others. While many are very good- including ourselves, we hope!- and we certainly wouldn’t tar them all with the same brush, the fact remains that there are some technicians and repair businesses out there that are lazy, don’t care about their work, can’t- or won’t- spend the money on the correct parts.
You Can’t Fix Everything by “Parts Swapping”
“Parts swapping” is a common technique in the industry. Essentially, this means that a lot of common problems can be diagnosed and repaired simply by swapping out major components with another (identical) one. If this solves things, that’s great- we know where the problem was, and the phone can go back together again. If not, we can try another.
Its popularity is obvious- parts swapping is a by-numbers approach to repair that doesn’t require in-depth technical knowledge and is effective in a large number of cases. In short, there’s nothing wrong with parts swapping as far as it goes.
The main problem is that it doesn’t always go far enough- parts swapping can’t be used for repairs needing board-level diagnosis and soldering as there are numerous small components making up a circuit.
It’s common for some stores whose skills are basically restricted to parts swapping to refer to anything that can’t be fixed this way as an “IC” fault. For example- power problem? “Power IC fault”. Camera not working? “Camera IC”. This applies whether or not the IC itself is actually at fault. For example, the board may have been perforated or shorted by someone using a screw too long for the intended hole. Or possibly one of numerous other causes not related to the IC- but the point is that you need to know more than parts swapping to figure it out.
You need genuine understanding and experience of electronics to fault-find correctly- otherwise you’re working blind and can end up turning a fixable problem into unfixable damage. Unfortunately, this can- and does- happen with inexperienced businesses that find themselves out of their depth.
One other issue with board-level repairs is that- unlike a parts swap- it’s often impossible to put things back exactly “as they were”, even if the problem is ultimately unfixable. Often you can get a phone coming in not working properly, but after a repair attempt it might not be working at all. This is the nature of some repairs, and we always try to be open with our customers about the risks and chance of success where this is the case.
We’re not miracle workers, but we do have years of experience- and the necessary technical equipment- that lets us deal with such damage properly, giving you a far better chance of your iPhone or iPad (or any other smartphone or tablet) being successfully repaired.
You Can’t Price a Board-Level Repair As If It’s a Parts Swap
The focus on the “parts swapping” approach can have an influence on pricing too. Many stores used to doing this decide how much money they want to make on the job (say, £10-15) and add that to the cost of the parts, depending upon what they’re swapping out. This is fine if you are doing a low-risk parts swapping approach and know there are likely to be a limited number of probable outcomes with little risk.
However, it isn’t a sensible approach if you’re pricing up more complex board-level repairs. Many people will see that an IC costs (say) £4 and assume that the repair can be carried out for £20 total or thereabouts. This doesn’t account for the fact that board-level repairs will typically take much longer than a parts swap- often several hours, much of which is diagnosis and soldering multiple small components using the microscope. (Each might- or might not- fix the problem).
There’s also generally a much higher element of risk- something that’s often impossible to judge accurately in advance, but which the repairer may be responsible for if it goes wrong. All this has to be allowed for in the price.
Skills, Experience and Training- You Need a Lot of Them
Generally, you can teach someone to swap an iPhone screen in a couple of hours. However, board-level repairs are a skill that has to be developed over many years- there’s no substitute for experience. There is a lot of training, research and personal development involved in keeping on top of these types of repairs and nothing stands still- every new device is different and needs to be learned about.
Apple purposely makes screen swapping relatively easy so they can offer this repair in-house. They can train someone to do this quickly. They don’t, however, make board level repairs easy- they don’t provide schematics, put underfill around chips that need removed, put components in difficult places to work on, or put shields over commonly replaced components to make it difficult to access.
In Short, Why Board-Level Repairs Cost More- and Why Ours Are Better Value Than First Thought
Those who don’t carry out board level repairs often don’t appreciate the time and risk involved, or understand that the cost of the component is usually just a small part of the total repair cost in such cases. Nor are they always aware how much training, experience and personal investment of time is necessary just to contemplate getting started on many repairs.
We have to bear all the above in mind when pricing up our board-level repairs. Whether you’re a regular or a trade customer, we hope you’ll understand why our prices for such jobs are more reasonable than they might first appear!
Conclusion
If you’re an iPhone or iPad owner with a faulty backlight or dark screen, bring it to us. We have years of extensive experience in phone, tablet and computer repair that gives us the advantage over “screen swappers” when it comes to more difficult problems like backlight circuit damage. We’re not always the cheapest, but we believe we’re the best value for money- we won’t cut corners, rush jobs or use substandard components, and we’re always as clear and upfront as possible. That goes for all our repairs- not just backlight issues, but also charging, battery and USB problems, as well as touch problems (including touch disease). Not sure what the problem is? Ask us!
If you’re a technician for another business looking to offload some trickier or more time-consuming jobs, ask us about our prices. You might be surprised just how affordable we are! Did you know that we also carry out Tristar (charging and USB IC) repairs and touch disease repairs as well? Again, feel free to ask us about our services!